Processus de production
Jeter un coup d’œil dans la centrale d’enrobage
Les enrobés sont produits dans une centrale d’enrobage. On distingue deux types de centrales : les centrales à enrobés continues et les centrales à enrobés discontinues.
En Belgique, la majorité des centrales d’enrobage fonctionnent selon le principe de la discontinuité, la production se faisant par lots. Le principal avantage de ce type de centrale est sa flexibilité dans la production de différents types d’enrobés. Dans le cas d’une centrale d’enrobage continue, la production se fait en continu dans un tambour mélangeur. C’est une bonne technique pour les grosses productions d’un seul et même produit. Si différents types de produit doivent être combinés, cette centrale est moins adéquate.
Dans l’explication ci-dessous, l’exemple d’une centrale discontinue est utilisé.
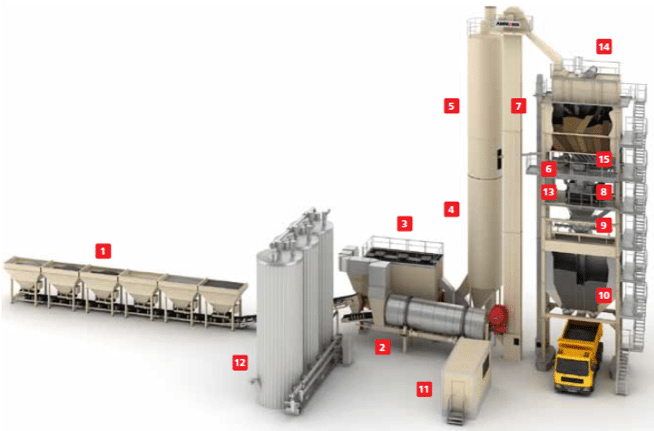
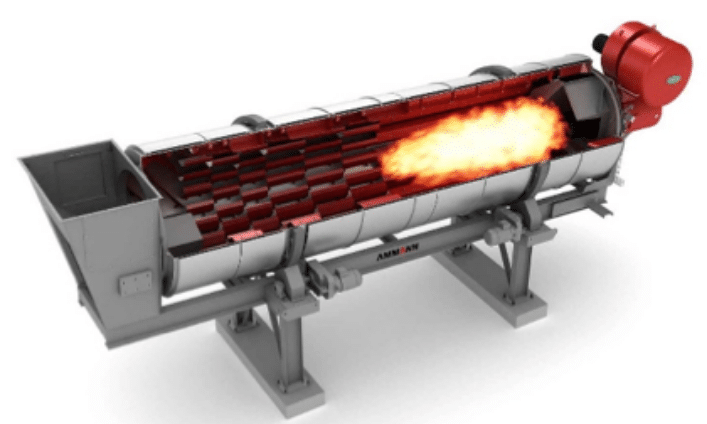
Les différents agrégats sont chargés à partir des stocks sur le terrain par une chargeuse à roues dans les prédoseurs (1). Chaque prédoseur peut doser un type/calibre différent de gravier concassé ou de sable. Un tapis roulant circule au bas du prédoseur, dont la vitesse peut être réglée. De cette manière, il est possible de doser plus ou moins de matière dans chaque prédoseur. Tous les agrégats sont transportés par une bande de collecte jusqu’au tambour sécheur (2) où ils sont séchés et chauffés à la température requise (environ 180°C à 200°C pour les enrobés classiques).
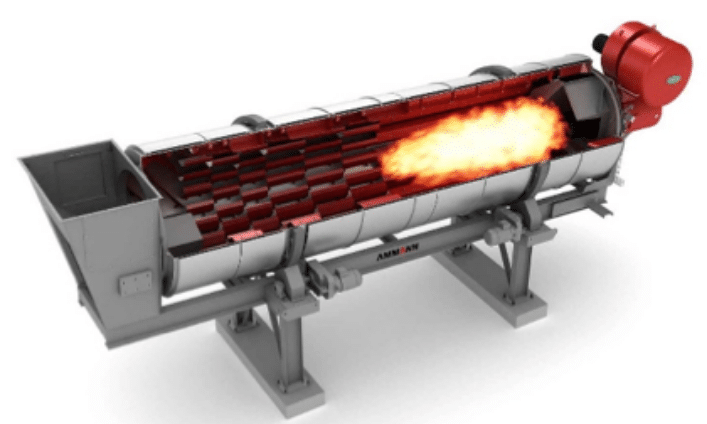
Le tambour sécheur est un cylindre rotatif avec à l’intérieur une série de plaques qui soulèvent les agrégats et les jettent à travers la flamme du brûleur afin de réaliser le processus de séchage et le chauffage des agrégats. Au cours de ce processus de séchage et de chauffage, une quantité de poussière, de vapeur d’eau et de gaz de combustion est produite. Tous ces gaz passent à travers une installation de filtrage (3), de sorte qu’uniquement les gaz propres et la vapeur d’eau soient émis par la cheminée.
La poussière qui est séparée dans cette installation de filtrage est appelée le filler récupéré. Ce liant est stocké dans le silo pour filler récupéré (4). Cette poussière est à nouveau dosée dans le processus de production de manière contrôlée. En plus du filler récupéré, il faut souvent ajouter du filler neuf . Nous stockons cette substance dans le silo à filler neuf (5).
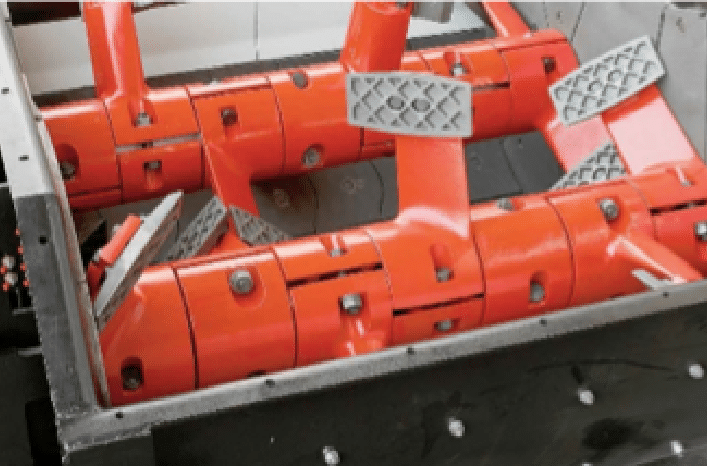
À la sortie du sécheur, les agrégats (sable et graviers) secs et chauds sont transportés jusqu’au crible (14) au moyen de l’élévateur à chaud (7). Sur le crible, les agrégats sont à nouveau séparés en fonction du calibre, puis stockés dans le stock à chaud (15).
En plus du sable, des granulats et du liant, nous avons encore besoin de bitume pour produire des enrobés. Le bitume est stocké dans des citernes (12) à une température moyenne d’environ 160°C.
En règle générale, pour chaque lot, toutes les matières premières doivent être pesées dans nos propres bascules (8) avant d’arriver dans le mélangeur (9).
Le mélangeur est constitué d’une trémie blindée dans laquelle deux bras rotatifs constituant de rames mélangent intensivement les matériaux. Ainsi, à une température moyenne d’environ 165°C, un mélange homogène est produit. Au fond du mélangeur, il y a une vanne qui s’ouvre dès que le temps de mélange est écoulé. Les enrobés entrent ensuite dans le silo à enrobés (10), d’où les camions peuvent être chargés.